Sanitary Blending Systems
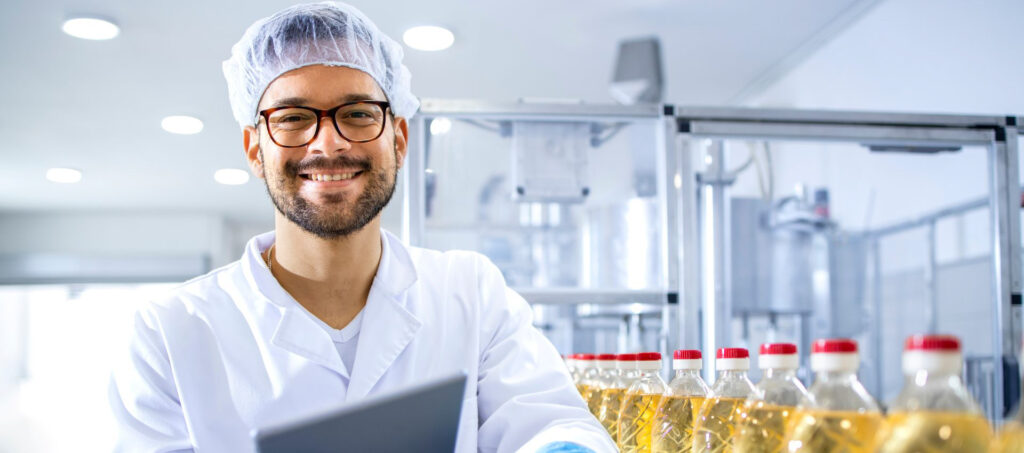
“Designed and Built to
FDA, AAA and ASME BPE Standards”
Welcome to the future of production efficiency! Our sanitary formulation system boasts unmatched quality and performance while keeping in line with safety and compliance with all regulatory standards. Transform your production process and minimize cleaning downtime with our industry-leading technology. AccuBlend’s sanitary blending systems are ideal for manufacturers of food, beverage, consumer products, industrial materials, and petrochemicals.
Our systems are fully sanitary and compliant with FDA, AAA and ASME BPE standards. All wetted parts are 316L stainless steel. All wetted parts have a 25 Ra internal finish. Our systems are fully drainable and fully CIP-able.
Blending System Components
Continuous Inline Blending Module
The Inline Blending Module is the heart of the on-demand formulation system. Each blending module can accommodate five ingredients to be blended together. For example, if blending of eight ingredients across all formulas is required, you would require two blending modules, one of which would have two spare slots for future ingredients to be added. These modules would be connected in series, serving a common inline blending header. The Inline Blending Module can be staged anywhere in your plant, but it should ideally be placed close to where the finished product will be packed out or loaded into tank trucks. This staging will result in minimum wash out volumes and minimum wasted product when switching to the next product variant.
Ingredient Dosing Pumps
Our ingredient dosing pumps are precisely sized for delivering each ingredient at an accuracy of +/- 0.5%. Our positive displacement pumps can deliver ingredients with a wide range of viscosities. Tight internal tolerances with no metal-to-metal contact between rotor and stator guarantee long service life for your ingredient dosing system between repairs.
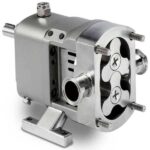
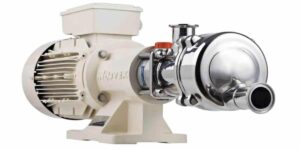
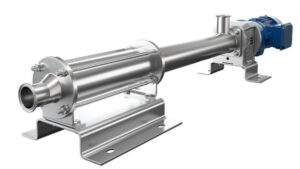
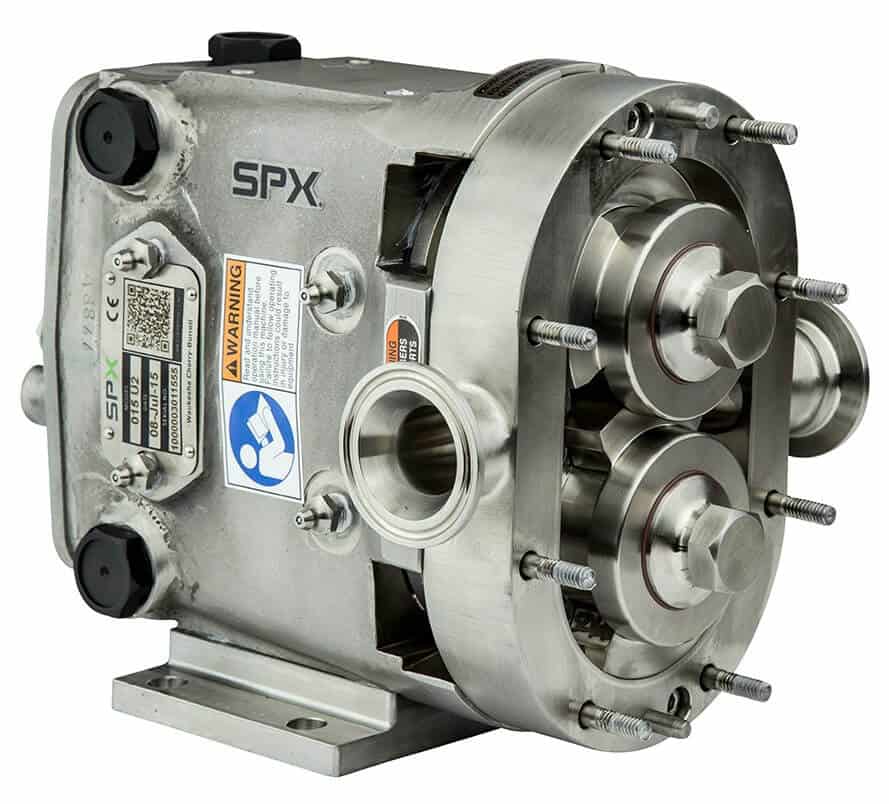
The following components are required for each unique ingredient.
Ingredient Dosing Mass Flow Meter
A Coriolis-type mass flow meter monitors the mass flow, volumetric flow and density (specific gravity) of each ingredient on a continuous basis. These values are reported back to the System Logic Processor multiple times per second.
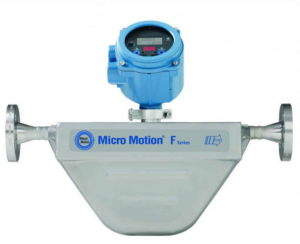
Automatic Ingredient Feed Shutoff Valve
At any time that Inline blending operations need to be paused or halted, the automatic ingredient shutoff valve will close upon command to do so by the System Logic Processor. This ensures that no additional ingredient can enter the header and also ensures that the Inline Blending Header contents cannot backflow into the ingredient delivery piping. Open and closed limit switches on this valve send feedback to the System Logic Processor that the automatic shutoff valve is indeed in its proper position.
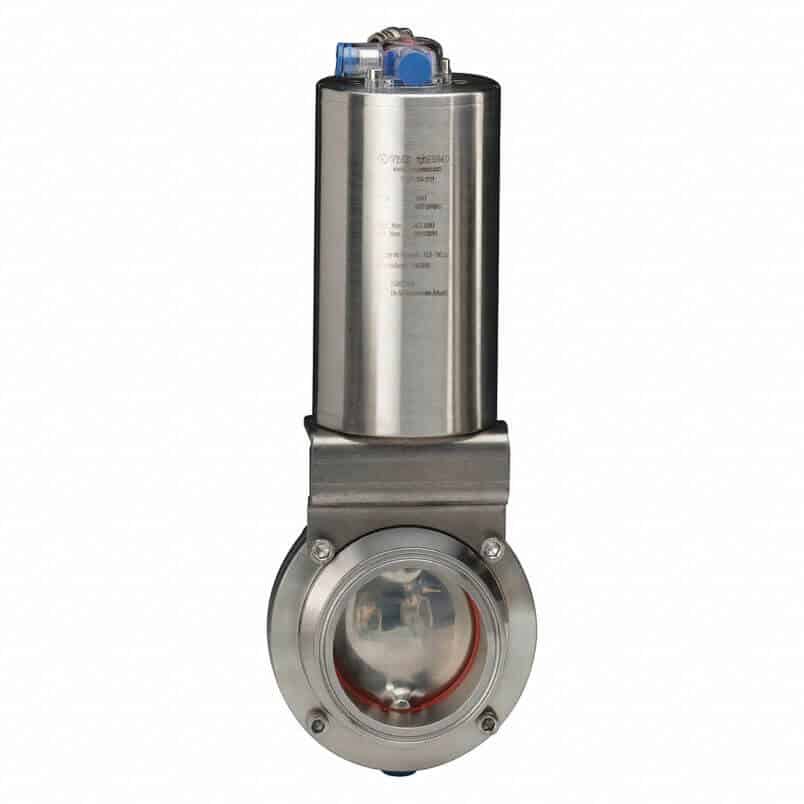
Ingredient Supply Check Valve
This spring-loaded check valve is located in each ingredient line right at the blend header tie-in point as a redundancy to what the automatic shutoff valve does as explained above.
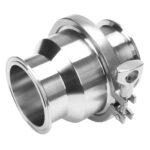
Main Control Panel
One Main Control Panel is required per system, regardless of the number of ingredients in your formula. The Main Control Panel houses the components listed below. The Main Control Panel can be located wherever you desire. It is typically sited at a location near the hub of where the operator usually circulates to perform their normal duties.
Logic Processor
The System Logic Processor is the heart of the monitoring and control of your inline industrial blending system. This processor executes a proprietary algorithm that updates multiple times per second to keep each ingredient flow within +/- 0.5% at all times.
In addition to monitoring and controlling the continuous blending system, the logic processor also functions as a recipe manager. Recipes for all finished product formulas reside in the System Logic Processor. New recipes can be added at any time via the Operator Interface Display or over your plant network.
The base system allows for the monitoring of all ingredient flows. Additional instrumentation can be included as listed under “Product Option Kits” below to monitor various parameters unique to your process. Operators may enter correction factors for each ingredient stream based on COA lab results if required. For example, if an ingredient typically has a specification of 16.5% active component and the lab results test that raw material at 14.1%, the operator simply inputs that data via the Operator Interface Display and the formula is adjusted accordingly.
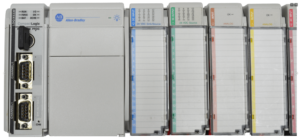
Operator Interface Display
The Operator Interface Display is a NEMA 4, 12″ color smart monitor built into the Main Control Panel.
Supervisor Functions
- Enter new recipes
- Upload/print Campaign Reports
Operator Functions
- Choose product recipe to run
- Check ingredient levels
- Enable system start
- Monitor system operation
- Respond to system alarms
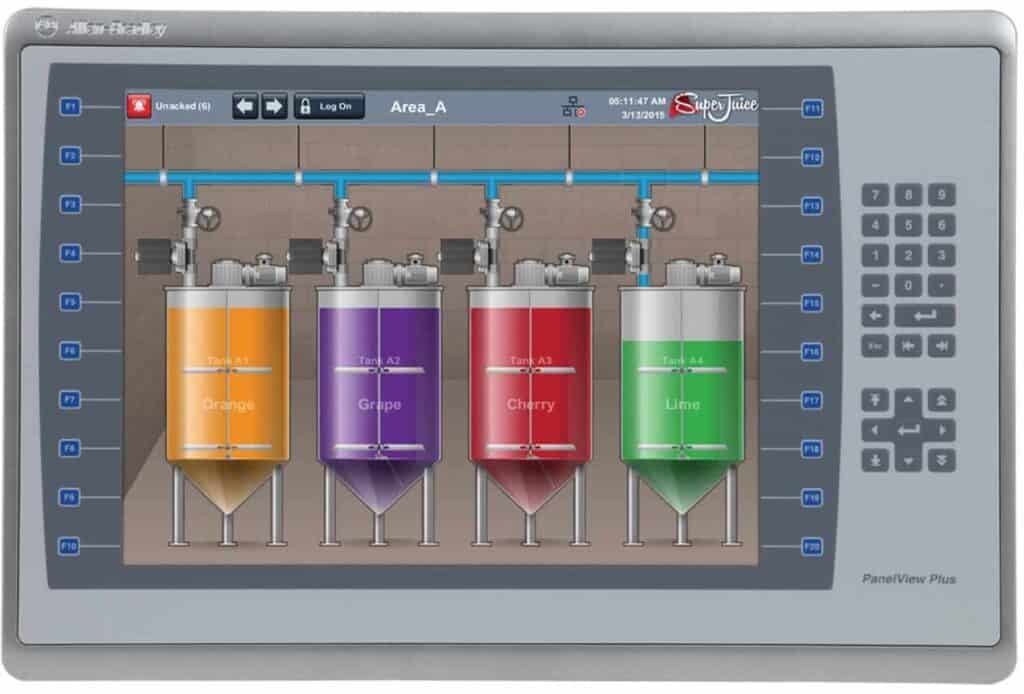
Main Fusible Disconnect
The main fusible disconnect serves as a safety device, providing overcurrent protection and a means to isolate the blending system from the power source for maintenance or repairs.
The disconnect switch allows technicians to manually open the circuit and effectively disconnect the equipment from the power supply, ensuring a safe environment for maintenance or repairs.
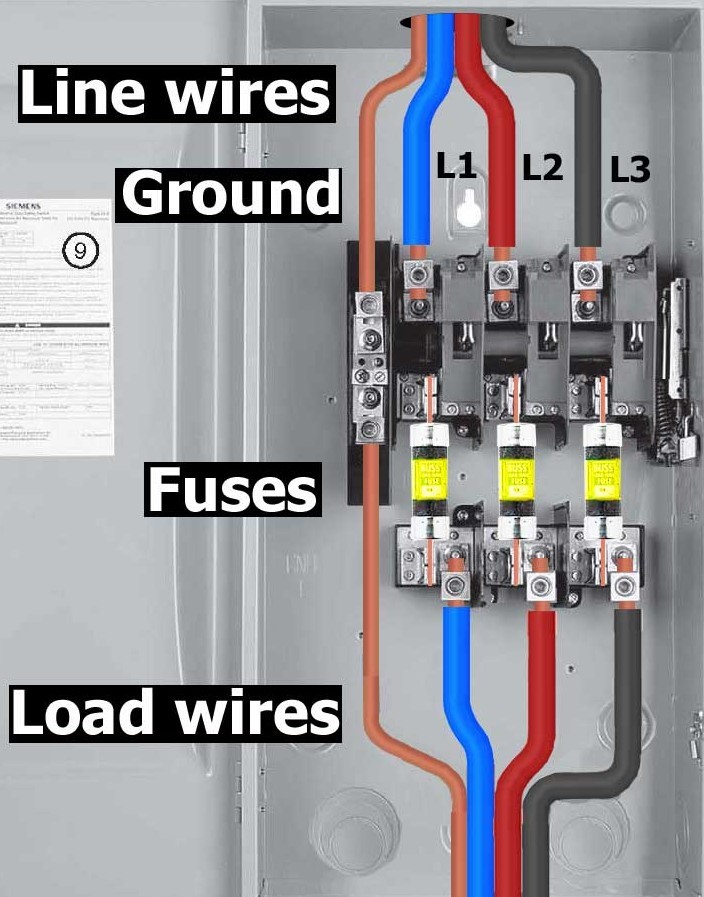
Emergency Shutdown Button
The primary function of an emergency stop button is to provide a quick and reliable way to shut down machinery or equipment when a hazardous situation arises.
When activated, the E-stop interrupts the power supply or control signals to the equipment, causing it to stop immediately.
After an E-stop is activated, the equipment will not restart until the button is intentionally reset, ensuring that the machinery remains safe until the situation is addressed.
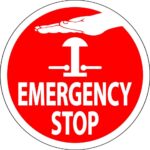
Food & Beverage Sectors
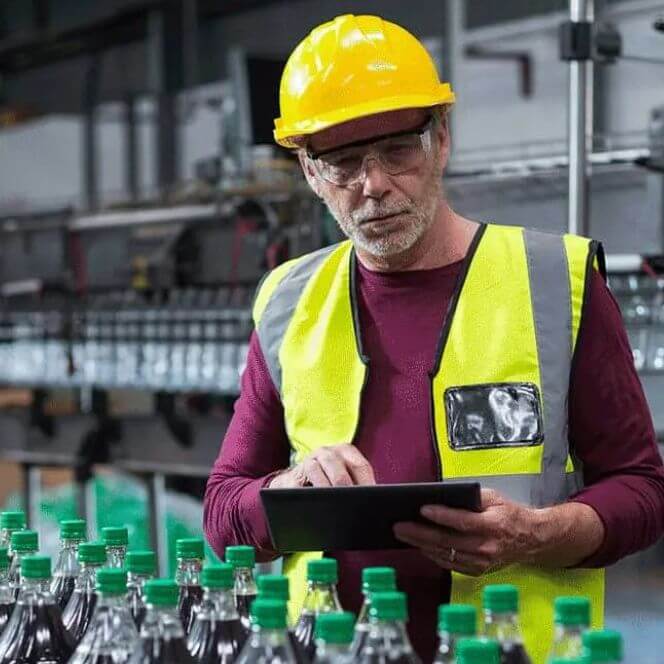
- Energy drinks
- Soft drinks
- Fruit juices
- Coffee drinks
- Flavored distilled spirits
- Pre-mixed cocktail drinks
- Blended spirits
- Dairy products
- Consumer Products Sectors
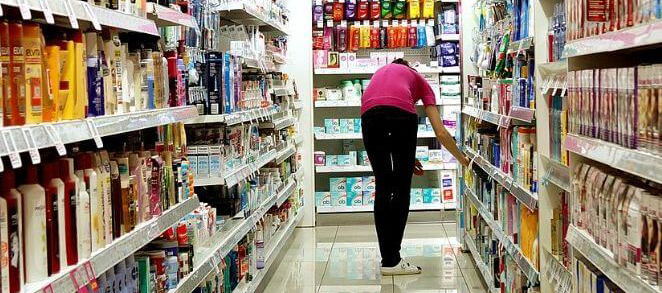
- Detergents
- Hard surface cleaners
- Soaps
- Candles
- Polishes
- Waxes
- Degreasers
- Cleaning products
- Air fresheners
- Shampoos
- Hair products
- Cosmetics
- Moisturizers
- Lubricants
- Paints
- Sealants
Our sanitary mixing system eliminates the need for traditional batch mixing, reducing the risk of cross-contamination and increasing overall production efficiency. Simply add a dosing pump, flow meter, automatic shutoff valve, and mix header check valve for every new ingredient added.
Take the first step toward enhanced production efficiency and quality with our cutting-edge sanitary formulation systems. Get in touch with us today to learn more about our products and explore how we can help you achieve your production goals.