Why Continuous Inline Blending
vs. Batch Mixing?
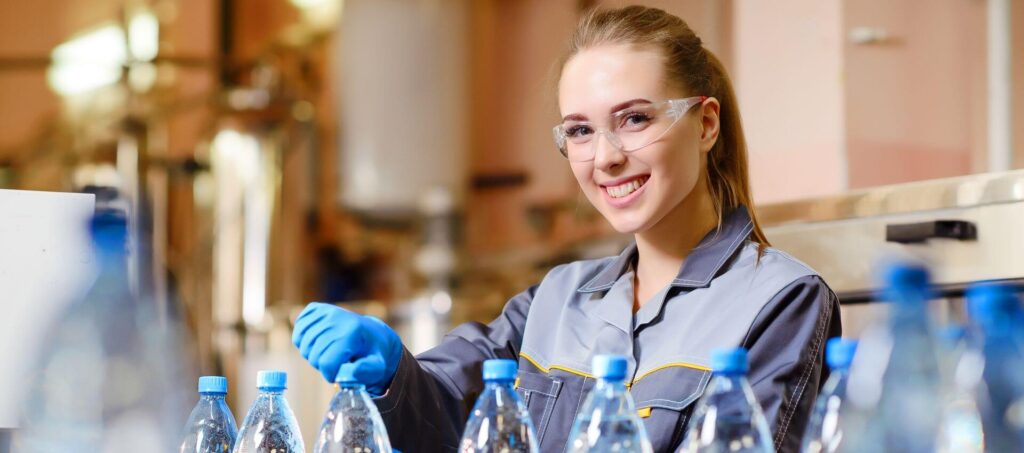
“More Time Producing Product.
Less Time Washing Out Batch Mixing Tanks.”
Increased Revenue
Increased Production Uptime
Spend more time producing product and less time washing out your mix tank! In traditional batch mixing, all ingredients are typically added to the main mix tank. After the batch is completed the mix tank must be thoroughly washed out before the next product variant can be made. This ensures that no cross-contamination of dyes, fragrances or allergens occurs. Wash out is typically accomplished through the use of spray balls located inside the mix tank. The wash out process can be quite time-consuming. This clean out time is time not spent producing product!
Lower Production Costs
Little-to-No Effluent Processing
In many cases, the washout contents cannot be sent directly to the municipal water treatment system. In these cases, it must first be treated at the client’s manufacturing facility. This can result in significant cost for treatment chemicals. When on-demand, inline blending is used as an alternative to batching, wash out volumes are greatly minimized, as only a short length of small bore header piping needs to be washed out.
In some cases, depending on the client’s specific requirements, this small volume of wash out contents can be blown forward into a small tote and re-blended into the next product variant at less than 1% of total formula. This can potentially eliminate all effluent discharge, resulting in zero emissions.
Reduced Staffing
System operation is fully automated. Operators can tend to replenishing raw materials and finished product filling operations.
The heart of the on-demand, continuous blending system is centered around accurate dosing of each raw material. Mass and volumetric flow of each ingredient is measured and reported to the logic processor many times per second. The logic processor incrementally adjusts raw material delivery pump speed to maintain flow that is accurate to 0.5% of the desired value.
Lower Capital Investment
Lower Total System Cost
In batch mixing, a new finished product storage tank is required for each new product variant that is added to a family of related products. This tank is typically 1-1/2 to 2 times larger than the main mix tank to allow a newly made batch to be transferred to a dedicated holding tank for eventual pack out of that particular product variant. The total installed cost of these product storage tanks can be significant.
Ease of Adding New Product Family Variants
When new products are added to your family of products, all that will be required is the addition of dosing pump, flow meter, automatic shutoff valve and mix header check valve for each new ingredient added.
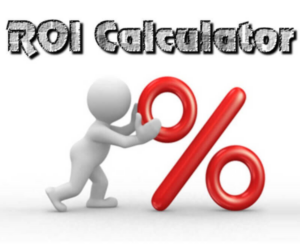
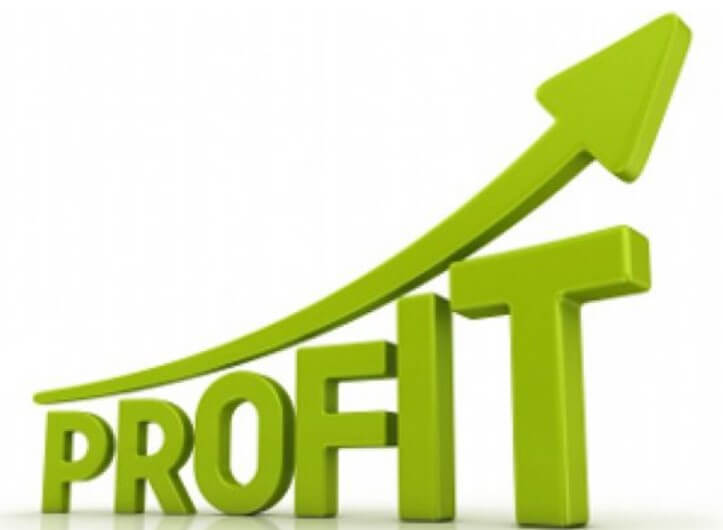