Inline Blending Technology
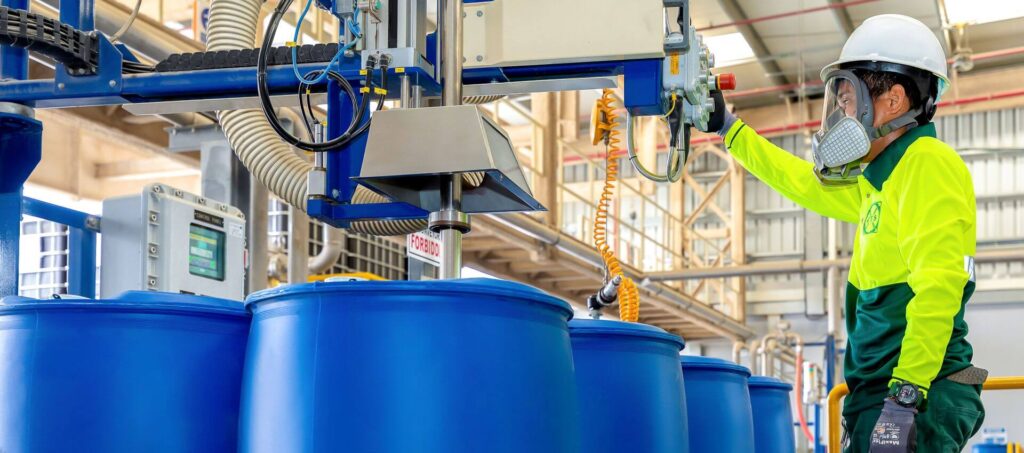
“Simplicity Is the Ultimate Sophistication”
Simplify and streamline your manufacturing process with continuous on-demand inline blending. The process provides efficient, cost-effective, and environmentally friendly solutions for producers of food and beverage products, consumer goods, industrial chemicals, and petrochem formulations.
Experience the power of a state-of-the-art logic processor at the core of the on-demand inline blending system. The processor receives real-time flow measurement signals for each ingredient addition, executes an advanced closed-loop control algorithm, and sends an output to a precise positive displacement dosing pump, improving the accuracy and efficiency of your production process.
Closed-Loop Ingredient Dosing Control
At the heart of the continuous on-demand inline blending system is a logic processor that that executes the following steps every 20 milliseconds (that’s 50 times per second!).
The processor receives a real-time flow measurement signal for each ingredient addition. It then executes our ModeChange (TM) proprietary closed-loop control algorithm and sends an output to a variable frequency drive which incrementally adjusts the speed of a positive displacement dosing pump.
Compared to other blending systems which use only traditional PID algorithms, our control strategy yields superior instantaneous accuracy, particularly in processes which restart repeatedly during a run or have little-to-no finished product buffer volume between the continuous blending system and the point of filling (rotary filler, downstream machine, tote fill line, drum fill line, tank truck, etc.).
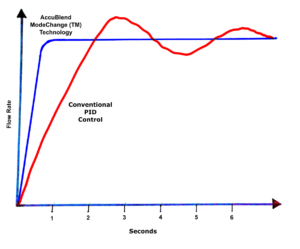
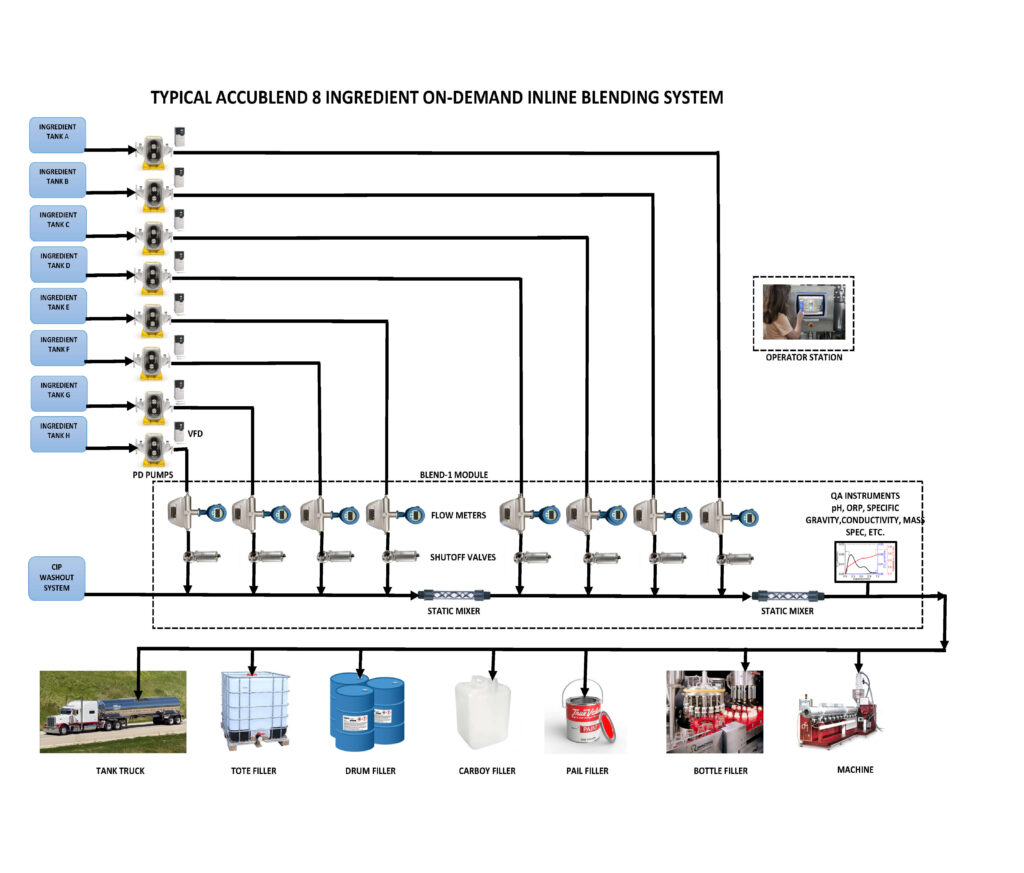
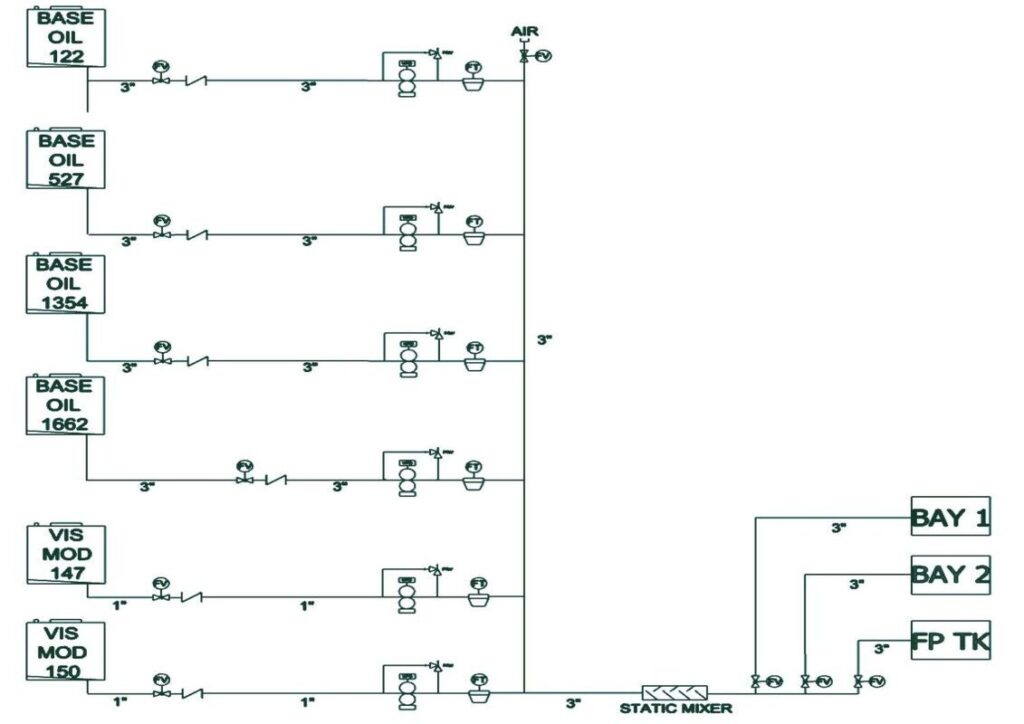
Thorough Inline Mixing
Thorough mixing is accomplished through the use of an inline static mixer. A static mixer with 24 elements will split the flow 16,777,216 times! In a small number of cases, more mixing energy may be required. This can be accomplished with the addition of an inline, motor-driven high-shear mixer. Finished product leaving the mix header is virtually indistinguishable from product made by traditional batch mixing methods.
Discover the advantages of continuous inline blending and mixing systems for manufacturers seeking efficiency, precision, and reduced environmental impact for food, consumer goods, industrial materials, and petrochemical production.
Unlock the potential of continuous inline blending and mixing. Contact us today to revolutionize your production process!
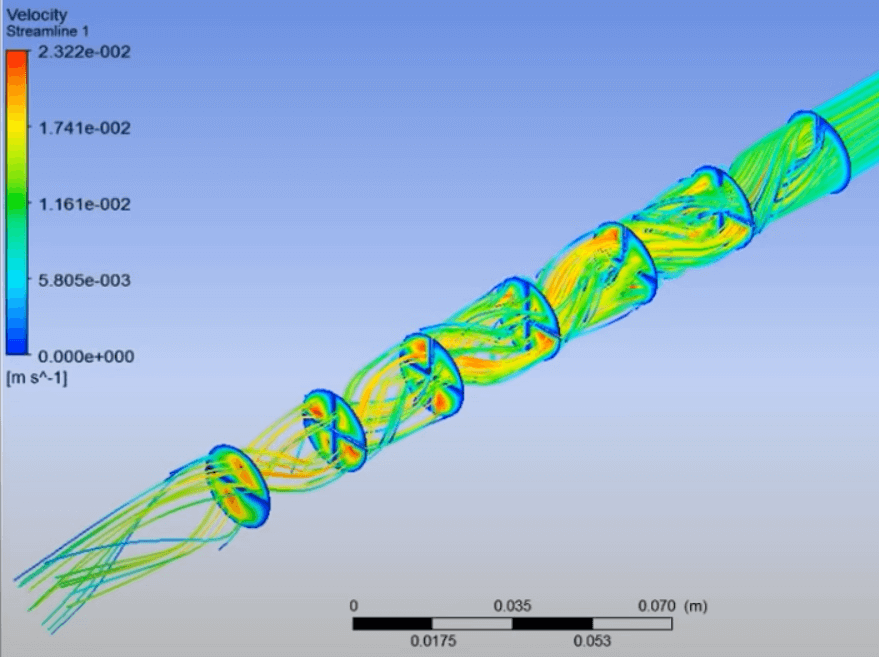