Why Choose AccuBlend?
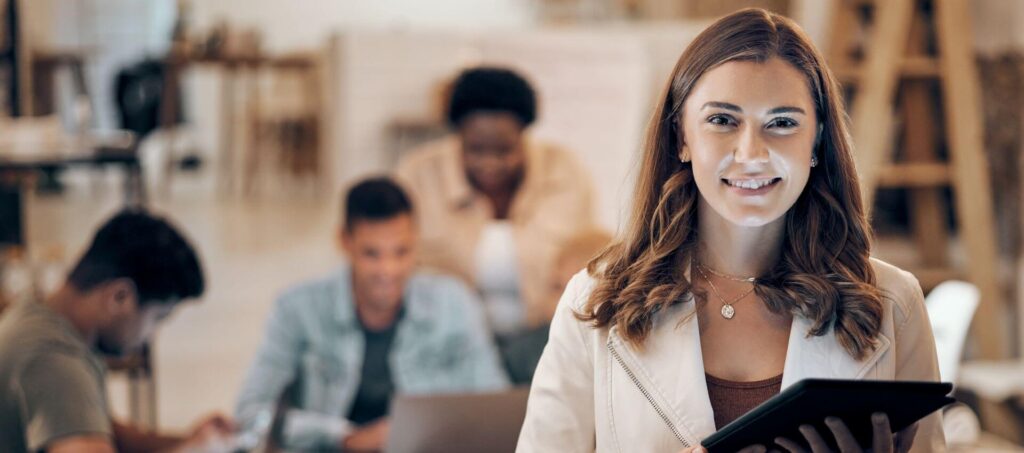
“Continuous On-Demand Blending Systems… That’s All We Do!“
Experience
With over 30 years of experience, AccuBlend Inline knows on-demand, continuous liquid mixing systems. We know when the technology can be applied successfully and when it cannot.
We have experience with high-viscosity fluids, non-Newtonian fluids, flammables, corrosives, low-solubility fluids, suspensions and emulsions.
Quality
Let’s talk about components first. Our component suppliers are a virtual Who’s Who List of industry-leading manufacturers. There are no off-shore, also-rans in the list.
On the fabrication side, quality construction means more than finding ”good “ TIG welders. It means having the systems and checks and balances in place to deliver properly crafted systems each and every time. Ask your potential blending system supplier if they can produce ASME documentation such as weld procedures, welder proficiency testing, MTR’s, weld maps, etc.
Value
We build products, not custom systems. Our products fit 90% of industry applications. The 10% of applications that do not should be implemented by competent companies that do design once, build once strategies.
Both approaches have their place. If our product approach is a fit for your application, we will inherently be a better value, as the cost of custom engineering will not financially burden your project.
Leadtime
Lead times are significantly shortened for product-based systems as compared with custom solutions, as there is no lengthy engineering phase required.
Safety
Delivering a system that is safe to operate and maintain is a result of multiple building blocks to ensure a strong foundation.
The first of these is specialized training. A system that is safe to operate is a result of bringing solid chemical, mechanical, electrical, programming and fabrication skills to the table.
The second is experience. Think about the wealth of things you have learned in the real-world manufacturing environment since you walked off stage, diploma in hand. Think of the evolution of what you did originally to how you would approach that challenge today. At AccuBlend, our engineers bring years of plant floor experience with them to ensure that your system is safe to operate.
The third is adherence to standards. Our systems are designed to meet ASME, NEC, FM and UL standards. These standards are the culmination of a consensus of the country’s top authorities in their areas of expertise.
The fourth is equipment and materials. As an example, at AccuBlend, we know where our tube, pipe, flanges, fittings and ferrules came from and we know how much chromium, molybdenum and nickel they are composed of. There are no off-shore, bargain basement corners cut when we spec and source our equipment and materials.
The fifth is journeyman-level craftsmanship. For example, TIG welding is both an art and a science. Not all TIG welders can produce equally good welds on piping that may be used in hydrofluoric acid service. At AccuBlend, our welders must pass proficiency on each type of weld they must do. This is not a one-time activity. That proficiency must be re-evaluated at regular intervals per ASME standards.
The sixth is commitment and conviction to do the right thing. The quality of all organizations is a reflection of the commitment and conviction that exists in the office of the CEO. Many organizations are good at setting expectations, but far fewer are good at enforcing those expectations under the pressures of competition, rising costs, availability of skilled craftsmen, etc. At AccuBlend, we do what is right and hold ourselves to a higher standard.
Unparalleled Customer Service
“100% Employee-Owned…. And It Shows”
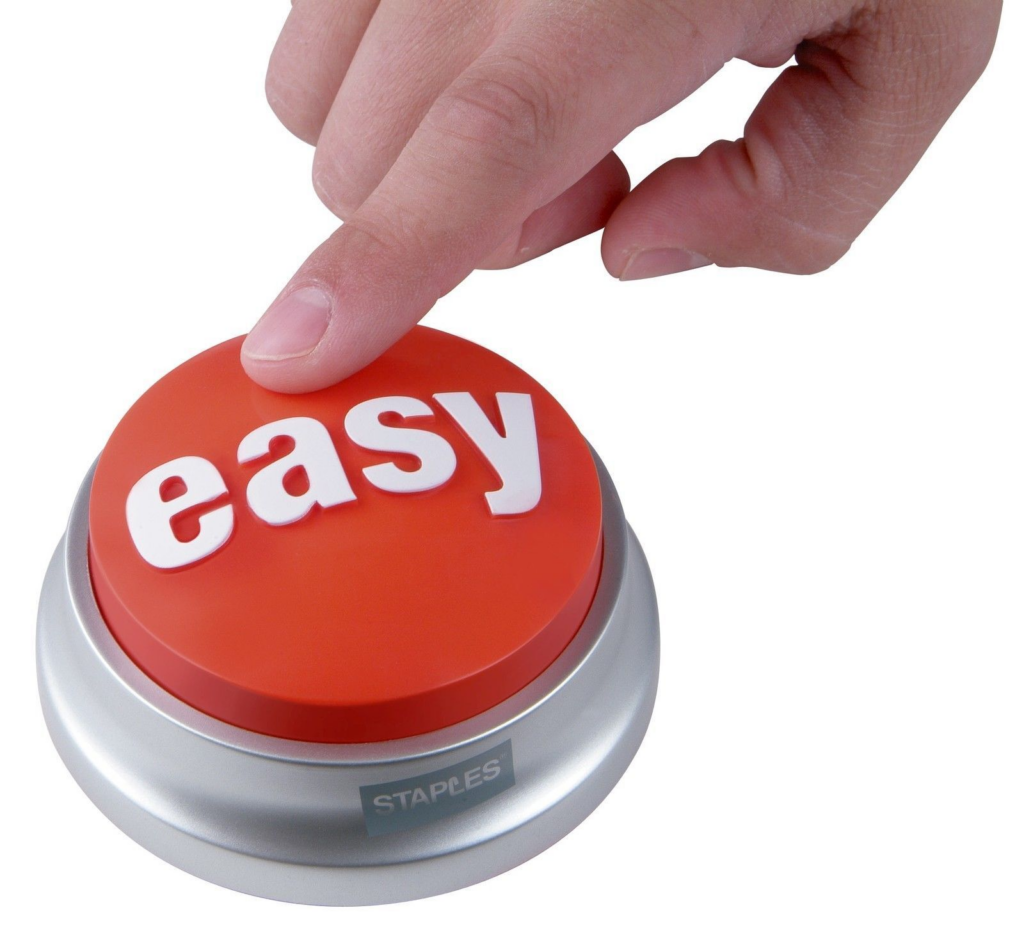
Every aspect of what we do is centered around making your life easier. Let’s look at what that really means.
It starts with your first contact with AccuBlend. When you visit our website, it has everything you need to know and no added fluff. Simplicity is the ultimate sophistication. The flow of the website is logical and you always know where you are. It’s written in plain English. Friendly and with personality, yet technically accurate.
How about when you try to reach us? How do we compare with other companies you have tried to contact? At AccuBlend, you chat with live human beings….. quickly. And the live human being always happens to be an engineer with real-world plant experience. There are no automated attendant experiences from Hell that eventually lead to nowhere.
Now let’s talk about our first conversation about your application. That’s easily accomplished by choosing “Talk to an Engineer NOW” or choosing “Schedule a Consultation Call” at a time that is convenient for you and your team. And… we don’t make you enter fifteen pieces of personal information to accomplish this.
That first contact will determine if continuous, on-demand inline blending is right for you. If it isn’t, we’ll tell you that. After about 20 minutes of discussion, we will provide you with a +/-5% capital cost number. That’s unheard of in the industry. How do we do that? Productization. There is no need to do custom engineering for each application that comes in the door. That work has already been done in support of standard equipment configurations. The logic programming has already been done. We are simply determining the proper pump and flowmeter sizing for each ingredient. You can already see where this approach has cost and lead time advantages as well.
Next, let’s talk about contracts. In a nutshell, they are written to be fair to you and fair to us. That’s how we roll. Our payment schedules are meant to keep both parties cash neutral for value and services delivered at any point in time. Great business relationships must be Win-Win.
Top 42 Reasons to Choose AccuBlend Inline
Key Decision Criteria | AccuBlend | Plan “B” | |
---|---|---|---|
1 | Available as lease-to-purchase? | ![]() | |
2 | System delivery less than 12 weeks? | ![]() | |
3 | Senior process/controls engineer on initial call? | ![]() | |
4 | System configured during initial consultation call? | ![]() | |
5 | Fixed bid price generated during initial consultation call? | ![]() | |
6 | System footprint known during initial consultation call? | ![]() | |
7 | Phones answered by knowledgeable human beings? | ![]() | |
8 | Critical spart parts list provided? | ![]() | |
9 | Industry-leading, name brand components used throughout? | ![]() | |
10 | Suitable for installation in NFPA Class 1, Div 2 hazardous area? | ![]() | |
11 | Fully automated operation? | ![]() | |
12 | Designed for minimum washout volume generation? | ![]() | |
13 | Zero-effluent capable? | ![]() | |
14 | Full material of construction analysis performed for chemical compatibility? | ![]() | |
15 | Simulation by Computational Flow Dynamics software? | ![]() | |
16 | Over 30 years of inline blending experience? | ![]() | |
17 | In-house blend testing lab? | ![]() | |
18 | Ability to provide online finished product QA parameter monitoring? | ![]() | |
19 | Ability to adjust ingredient add rate to account for raw material lab analysis? | ![]() | |
20 | Campaign data collection for each production run? | ![]() | |
21 | Password-protected new recipe generation? | ![]() | |
22 | Unlimited recipe generation and storage? | ![]() | |
23 | Minimized system footprint? | ![]() | |
24 | Minimized system washout duration at product variant change over? | ![]() | |
25 | Designed in the USA? | ![]() | |
26 | Ingredient dosing accuracies to +/-0.5% for flows from 0.1 gpm to >100 gpm? | ![]() | |
27 | All wetted parts 316L stainless steel? | ![]() | |
28 | Designed and built to these standards? | ![]() | |
29 | —ASME BPE Biopharm | ![]() | |
30 | —Fully drainable | ![]() | |
31 | —Fully CIP-able | ![]() | |
32 | —20 Ra wetted part internal finish | ![]() | |
33 | —Zero dead legs | ![]() | |
34 | —ASME B31.1 pressure piping code | ![]() | |
35 | —NFPA Article 230 | ![]() | |
36 | Remote monitoring and alarm notification of key production personnel? | ![]() | |
37 | Built by journeymen craftsmen in the USA? | ![]() | |
38 | Mechanical & Electrical Installation Prep Packages supplied for field contractors? | ![]() | |
39 | Failsafe power and control design? | ![]() | |
40 | System designed by Board Certified Professional Engineers? | ![]() | |
41 | System commissioning performed by degreed engineer? | ![]() | |
42 | Remote troubleshooting possible via secure network connection? | ![]() | |