Frequently Asked Questions
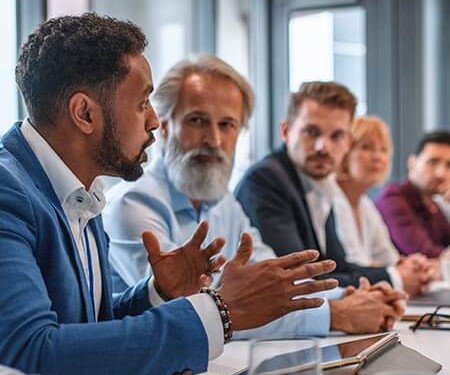
“Clarity of Communications Breeds Success for All Parties“
Technical
How can I be assured that the system will not malfunction, thus producing thousands of cases of off-spec product will then have to be quarantined/reworked/destroyed?
The flow of each ingredient is reported back to the controller many times per second. If for any reason the actual measured flow rate does not match the commanded setpoint (line blockage, ingredient supply tank ran dry. etc.), the blending system will shut down and an alarm will sound. Thus, no off-spec product will be made.
Can the inline blending system compensate for raw material ingredient variations?
This can be accomplished in one of two ways.
- Based on lab QA analysis, the lab can report actual efficacy and a “calibration” factor can be adjusted prior to the start of the run. This testing should be redone each time a new lot number of that particular ingredient is added to the ingredient supply tank.
- If variations in ingredient feedstock characteristics change more rapidly, instrumentation can be added to measure key finished product parameters (viscosity, density, specific gravity, pH, refractive index, spectral response, color, etc.) in real-time and ingredient flows can be incrementally trimmed on an ongoing basis.
How much involvement will be required of the operator in using this blending system?
Once the operator enters or selects the desired formula, the system is started and runs in a totally automatic mode. Proper dosing is constantly monitored and the system will shut down if any ingredient is not being delivered at the proper rate. The operator can focus on other duties such as raw material replenishment and staging, packaging line operation, etc.
How do I clean out the system between product family variant changeovers or when the system is shut down for extended periods?
The base configuration will permit the attachment of a washout/CIP system to rinse out the small-volume common finished product header. The washout/CIP system can be by others or supplied by AccuBlend. Various washout/CIP strategies and chemistries can be supported (water-based, solvent-based, quaternary compound-based, etc.).
My internal management team, as well as my customers, require documentation for assurance that good quality product is produced and that there is traceability in the event of a product recall. Can you provide this?
The AccuBlend control system will collect all desired production run data and store that information for historical record of key parameters and lot traceability.
Can your system blend dry materials?
When a client has dry ingredients, we recommend incorporating those ingredients into one of the liquid ingredients to form a premix.
Some of my ingredient storage tanks are located hundreds of feet from where we wish to blend. Is this an issue?
Not a problem. In these cases, the ingredient dosing pumps are located at the ingredient storage tank, rather than on the blending module itself.
There is talk that we will be adding future product family variants in the coming years. Will your system support this?
Absolutely! That’s part of the advantage of modularization. Future product variants can be added with ease.
Can the blending system be made portable (mobile or easily relocated)?
Yes. Our engineers will look at your specific needs and requirements to arrive at a configuration that will fit nicely into your plant.
Many of our ingredients are viscous and so are our finished products. Will your system work for these viscous materials?
If all of the ingredients are “pumpable”, we can typically implement continuous inline blending.
We have even done applications involving solid shortening and butter, utilizing auger-fed progressing cavity pumps.
Our packing line has many short stoppages throughout a shift to clear filler jams, make equipment adjustments, etc. Will this be an issue when using continuous inline blending?
While starting and stopping an inline blending system regularly is possible, it’s always advisable to start it and let it run indefinitely in equilibrium. For situations where there are many brief stoppages downstream of the continuous blending system, a small “buffer” or “surge” tank can be provided between the blending system and the downstream processing equipment.
Commercial
We are standardized on different component brands than you offer. Can you use the brands we normally use in our plants?
AccuBlend can supply systems with component brands that you are standardized on, provided our engineering team determines that they meet the same specifications as the components we normally specify. The only components that we will not consider substitutions for are the Programmable Logic Controller and the Operator Interface Display, as both require considerable software programming.
What is the payment schedule?
50% is due at the time of order. All equipment and components will placed on order upon receipt of this down payment.
35% is due prior to shipment. Your system will be shipped upon receipt of this second payment.
The final 15% payment is due at the conclusion of commissioning by an AccuBlend engineer at your plant site.
We consider our products to be ultra-proprietary and are concerned about releasing ingredient and formulation information to third-party suppliers. How can we be assured that this information will stay top secret?
Signing client Non-Disclosure Agreements (NDA’s) is part and parcel of our business. We take the protection of your intellectual property very seriously.
Does AccuBlend do field installation?
AccuBlend will supply a Mechanical Prep Package and an Electrical Prep Package to you shortly after order placement. This package can be used by your field installation contractors to put any minor plant infrastructure (power drops, interface to existing plant raw material systems, wash out system connection, etc.). in place prior to the arrival of the blending system.
How are your systems commissioned?
All systems will be Factory Acceptance Tested (FAT) prior to shipment. Full system functionality will be verified at our plant
Upon completion of installation at your plant site, AccuBlend will send a competent engineer to your site to commission your blending system. This commissioning phase consists of the following.
- Verification of proper interface with existing plant systems (mechanical, process and electrical).
- Operator training
- Maintenance training
- Verification that system performance meets or exceeds all desired parameters (production rate, dosing accuracy, etc.).
- Resolution of all punch list items.
How will the price of your system compare with a traditional batch mixing system?
Intuitively, there are clear advantages on a capital investment basis alone. All large mixing and storage tankage goes away ($$$$$). With it go other associated costs (tank farm expansion, agitators, bulk storage heating equipment, etc.).
How will the price and lead time of your system compare with other continuous blending suppliers?
All system manufacturers are under the same constraints concerning component lead times (pumps, flow meters, valves, static mixers, etc.)
Having said that, since our systems are productized and pre-engineered, there is little or no “custom” engineering required. This can easily shave four weeks off of system lead time as compared with custom systems.
We have been burned in the past by buying equipment from suppliers that have incorporated less-than-industrial-quality, offshore components in their systems, resulting in much downtime, missed shipments and considerable equipment replacement cost. Are your systems superior in this respect?
Our components are of the finest pedigree, a virtual Who’s Who List of market leaders. We use only top drawer componentry in our systems, as noted below. Our components are made in the USA and are readily available through extensive dealer networks throughout the country.
We have limited space to install a blending system. How much space is needed for your system?
In general, our blending modules are very compact. The footprint of a five ingredient blending system is approximately 10 foot by three foot. Upon understanding your space limitations, our systems can be re-configured to meet those requirements in the vast majority of cases.